Hanza Crest Apartments - Hyderabad, India
Bhavana Reddy
Construction Management
General Building data
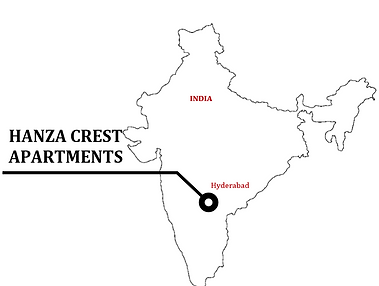
Building name: Hanza Crest Apartments
Location and site: Jubilee Hills, Hyderabad, India
Building Occupant Name: Multi Families
Occupancy type: Residential Purpose
Size: 56,000 SQFT
Number of stories above grade and total levels: 5 Floors above grade and
2 floors below grade
Project delivery method: Design-build
Dates of construction (start – finish): November 2014-June 2018
Actual cost information: The construction cost amounts to a little over Rs. 70,000,000. This converts to $1.05 million according to the conversion rate of 1 INR= 0.015$, as of October 3rd, 2016. The owner as per the current status of the project provided the construction cost.
Primary Team:
Owner: Ambience Constructions (Owner’s representatives)
Construction Managers: Ambience Constructions
Architect: Finger 6
MEP and Structural: SS Infrastructure Project consultants
MEP and Structural Engineers: Ambience Constructions
Hanza crest apartments are built in a residential zone. They are under construction on a rectangular site. The site was initially acquired with rocks and had to be excavated approximately 8770.6 yd3 . This building is designed for residential purpose
only. It is located in a complete residential zone of the suburban area. The
building consists of 1 cellar and sub-cellar parking garages and 5 residential
floors. Each residential floor consists of 2 three-bedroom apartments
as per owner’s requirements. The building has external wooden cladding
for architectural purpose.
Hanza crest apartments follows Indian Standard Code
Building façades: The building enclosures in India typically consists of concrete walls due to weather constraints and security purposes. The same applies to Hanza crest apartments. The façade consists of concrete walls with plastering and waterproof paint. The northern façade has a wooden pattern external cladding and structural steel railing and toughened glass railing. The eastern façade only consists of wooden pattern external cladding, while the western and southern view of the Hanza crest apartments project mere overhangs above the glass windows.
Roofing: The roof slab is a typical concrete slab that consists of an asphalt sheet between slab concreting for waterproof purposes.
The owner is not opting for a LEED certification for this project. There is some landscaping done on the 3 feet wide-open space around the building.
PART 2
Excavation
Excavation is one of the longest and critical phases for this project. Located in a residential zone, the project had constraints with the usage of blasting. Since the zone Hanza crest apartments located had a height restriction, the land had to be excavated to a depth of
22 ft (8770.6 cu.yd) as mentioned earlier, for basements purpose.The entire main site underwent excavation. The excavation phase started from south to north.The project’s site was excavated by chemical blasting with restrictions and JCB bucket equipment. The entire site is divided into 3 sections to show from which part the excavation is started.
Construction (Means & Methods)
Hanza Crest apartments are entirely made out of steel and cast in place Roller compacted concrete (RCC). This is highly durable and typical in India. The cast in place is preferred in India for most of the residential buildings due to the labor cost in India which is very cheap and avoid transportation charges. Ambience Construction firm utilized the land opposite to the main site for different purposes at different phases.
There are two types of form work used for the structural system, Metal sheets and plywood.Most of the construction is done with metal sheets which are prefabricated in different sizes. Plywood is cut and used as form work only when there are irregular sizes. Metal sheets are also re-usable and more durable.
The concrete was made and pumped out of ready mix concrete plant, batching plant and manual concrete mix plant based on the requirement. Along with the concrete trucks, curing tanks, vibrators and cement mortars are also utilized.
After the superstructure phase, the building finishes and enclosure are scheduled. Material hoist is used for easy delivery of materials to each floor. The finishing sequence is floor wise. There are other external developments for this project which includes landscaping, external and podium lighting, security and access control system and solar fencing.
Structural System
As mention earlier, the structural system of this project is made of steel and cast in place Roller compacted concrete (RCC) which is very typical in India due to its high durability and strength.This type of concrete does not require joints. A typical apartment is made of concrete columns, slabs and beams.
Hanza Crest apartments is constructed on a typical raft foundation made of reinforcement, and Portland cement concrete (PCC) with different ratio mixing based on the requirement. The foundation consists of rafts and column footings which distributes the load evenly. M25 concrete was used for foundation which has a compressive strength of 3500 psi.
For the superstructure of this project, the reinforcing bars are pre- fabricated and are delivered on site. These reinforced bars are bind together with stirrups on the required day. For the columns, thermos mechanically treated (TMT) bars s which have resistance towards steel corrosion with a Fe500 grade and Mild steel bars are also used but very minimal for columns.
The columns are filled with concrete with the usage of metal sheets form work. The concrete is cured with the help of vertical props. M35 grade of concrete which has a strength of 5000 psi is used for all columns and slabs.
Mechanical System
Most of the buildings in India do not acquire mechanical system. Based on
the occupant’s requirement, wall units are fixed.
Bio-metric plumbing system is applied to Hanza crest apartments. The water
acquired from bathrooms is sent to sewage treatment plant to purify it and used for gardening and bathrooms in staff rooms. This system is productive for the building
and helps to reduce the water scarcity in India.
Lighting & Electrical System
The electrical system is similar in most of the residential buildings in India.Standard electrical points are fixed. Each bedroom is facilitated with electrical points fan, Air conditioner, and two lights. There is diesel based-run generator that supplies to the apartments in the situation of power-outrage.
Architecture
Enclosure
Sustainability Feautures
Code

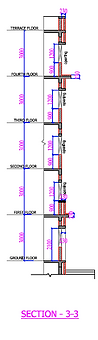
Figure 1: Building Elevation
Figure 2: Front Elevation with wooden cladding
Figure 3: Eastern façade mechanism

Figure 4: Erection of Columns (Site picture)
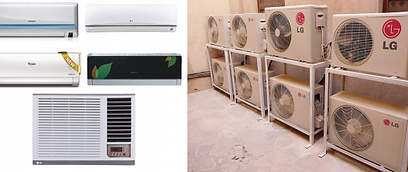
Figure 7 : Typical air conditioners (AC) used in India (Wall) and
External Unit of AC (Right)

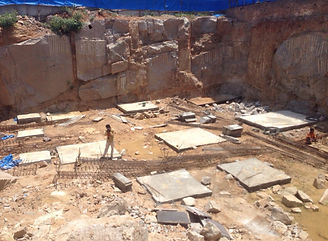
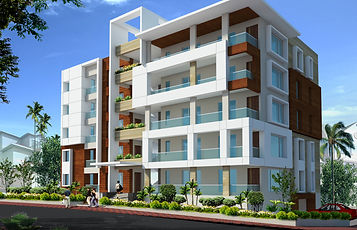
Figure 3: Main site after excavation (Site picture)

Figure 5: Use of metal sheets for form work (Site picture)
Figure 6: Steel and RCC structure (Site picture)